Going into the final week (which is absolutely crazy to think about), I just wish there was more time. Six weeks seems like a long time, but they have gone by so quickly. I’ve learned about engineering design, different cultures, global health, and have made many new friends across the world. It’s been an incredible experience thus far, and this week was one that was particularly inspiring. It made me really consider where I can take this experience and this opportunity. How can I learn from it? How will this inform my career choices?
One of the workshops that truly struck me this week was by Ms. Faith Mzandu, the co-founder of WomEng Malawi. She talked a lot about the challenges that she had to overcome as a woman in engineering — seeing herself as the only woman in STEM classes, with no female mentors around. Witnessing backhanded comments about her abilities. Feeling that her contributions weren’t as valued as her male counterparts. Even though I am not from Malawi and don’t have nearly the same background as Ms. Mzandu, I related to all of it.
Being a woman in engineering, as early as high school I would see all of my STEM classrooms filled with all male students, with just a handful of girls. Additionally, a main issue lies in how women tend to internalize these comments. My male friends seem consistently more confident than I am before taking an exam or doing a presentation. Even with the same amount of preparation, women statistically see themselves as not up for the job — not qualified enough. Ms. Mzandu encouraged the women engineers on the call to find female mentors, find people that we could look up to. She also made a point to the males on the call: if a female is being mistreated in the workplace, recognize it and speak up about it. Small comments can make the biggest difference.
Ms. Mzandu’s talk gave me more confidence about being a woman engineer, and also made me appreciate the women in STEM that I know that much more. Looking at the participants on the call, the majority were women. And looking even within my own team, there are three women engineers. It’s empowering to be in this environment, where women’s voices are encouraged and admired. It was a really powerful final stakeholder to speak to, and a talk that I won’t forget.
The rest of the week consisted of a few more workshops, but a lot more group work time. This coming week we have pitches and presentations to key stakeholders and donors each day. We started the week honing in on our final solutions to the two prototypes.
For the UVC disinfection system, after many iterations of brainstorming and bouncing around different ideas, we settled on four final suggestions to the current design. First, we want to make the new shape of the system half the size of the original circular clothesline design. Creating this half-circle orientation, the system will take up less room, and will cost less (with the smaller system, 3 bulbs will be used instead of the original 5 bulb setup). However, to maintain the mask capacity of the system, we propose having a two-layer clothesline.
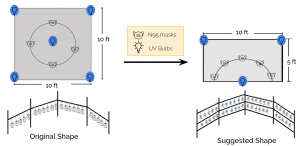
Based on stakeholder feedback, we also realized the need for concrete tests of system efficacy. We ultimately decided that both a viral load test and a filtration test was necessary. The viral load test would be tested based on dosimeter card readings (dosimeter cards change color when the necessary dosage for disinfection is reached). Filtration quality will be tested based on a smell test — by aerosolizing different smelly substances, mask wearers can test whether they can smell the chemical with the mask on. If they do, then the mask doesn’t filter properly. Finally, we suggest adding a feedback mechanism to show when the system is in progress, and we also suggest imposing a screening process where soiled masks (with makeup, etc.) cannot be disinfected. A potential idea to mitigate this is to also provide a thin, breathable fabric in the mask, such that the makeup and cosmetics will land on the disposable fabric, not on the mask.
With this prototype, we also have two new project proposals for future Rice 360 teams. We first suggest creating a smaller UVC “box” that could be used in more low-resource, rural settings. This could be simply a cardboard box with reflective surfaces on it and small UV bulbs on the corner. However, with this proposal, we also want future teams to look at alternate power sources like solar panels. This “box” could be adaptable and flexible to different hospital settings, as we have now realized that these systems are not one size fits all. We also propose a project for 360 teams to make cheap, affordable UV light meters for places like Malawi that don’t have access to them. Homemade light meters can cost around $10, but the ones that users can buy online cost as much as $1000.
For our second prototype, the face shield design, we came up with one finalized design recommendation. For these recommendations, we thought critically about the stakeholder feedback we had received. We focused on a comfortable piece that could connect the shield to the forehead, and a comfortable head attachment mechanism that could be reused. Building on the initial foam model, we now suggest having a laser cut plastic shield with curved edges. On these curved edges, we are suggesting adding small hooks where a removable elastic head attachment piece can be added. By making this removable, the elastic can also be machine washed, and the laser cut plastic can be cleaned with disinfectant. For the forehead attachment, we suggest keeping the foam model, but adding a machine-washable foam enclosure. This Chitenge fabric enclosure (fabric commonly found in Malawi marketplaces) can cover the foam with a zipper, and can then be attached to the shield with velcro. Velcro pieces can be sewn onto the Chitenge fabric, and can then be attached to the velcro attachments stapled onto the shield. By using solely velcro, foam, and Chitenge fabric, all of the materials are locally sourced and can be made with materials directly available in Malawi. This design will also maintain the comfort that the clinicians wanted, while also making the shield reusable.
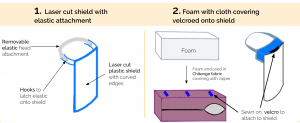
Once we finalized our suggestions, we worked on creating presentations and pitches to prepare for the upcoming week. We focused on graphically representing our ideas as much as possible, as the UVC system especially could be hard to conceptualize without visual aids. After finishing the slides for our presentation to the design studio managers, we recorded a video summarizing the work we have done so far for design studios in Malawi. Playing these videos back, I’m really proud of the work that my teammates and I have done these past 5 weeks. I truly believe in the ideas that we are presenting to the design studio managers. While I feel some sadness that this amazing program is soon coming to an end, I’m really excited to see the responses of the design studio managers and some of the Rice 360 donors later next week!
– Bhavya 🙂