Content warning: My project deals with pediatric sexual abuse. Please take care of yourself and feel free to forgo reading any parts of this blog.
The name of the game this week was divide and conquer. At the end of last week, team PIPER spent time prioritizing and delegating tasks to ensure we would finish our project on time. As a result, we dove into this week focused on accomplishing our individual goals related to the project. For me, this meant figuring out the attachment mechanism for attaching the labia and hymen to the base. Dr. Wettergreen had suggested looking into a bayonet mount, so I created a bayonet mount on Fusion 360 and 3D printed it. However, due to the oval geometry of the anatomy and the need for the model to rotate, the bayonet mount proved to be ineffective in correctly locking the labia and hymen to the base.

This is the bayonet mount that failed to attach the labia and hymen to the base.
While I was trying to create the bayonet mount, my teammates were hard at work on other aspects of our pediatric pelvic model. Alex focused on extending the labia and hymen mold, as our client had requested we make the anatomy an oval shape, as opposed to the current circle shape. This would give nurses more skin with which to practice performing labial traction. Elise and Shivani focused on further materials testing. After receiving a shipment of Soma Foama, they tested this material to see if it could be used in creating the estrogenized hymen. However, this material was very fragile and ripped after slightly pulling the material apart, causing us to remove it from further materials consideration. Elise and Shivani also created separate hymen molds to create hymens that could then be attached to the labia.
At this point in the week, I was feeling frustrated with how things were going, as we seemed to be struggling with every aspect of the project we were working on. The bayonet mount failed, Alex was struggling to edit the current labia mold, and our Soma Foama ripped when molded. Then, we had our client meeting, which caused a pivot in our plans. Ms. Harris decided that she did like the circular shape for the labia and hymen instead of the oval shape, making our lives easier by allowing us to use the circular LUCIA labia mold instead of trying to edit it into an oval. Additionally, we met with Grant, the chief designer for Rice 360, after the meeting, and he gave us a promising idea for the attachment mechanism. While it was tough to pivot and scrap our work for the week up until this point, we knew that this was the way to move forward in order to complete the pediatric pelvic model.
After these meetings, Shivani and I got to work on creating the new attachment mechanism. The mechanism consists of three pieces- a cylinder with a rectangular hole in it that is permanently attached to the base of the model, a table with the labia and hymen and a rectangular protrusion that fits into the hole in the cylinder, and a ring that screws on to secure the two together. The attachment mechanism functions most similarly to a Mason jar- one places the labia and hymen into the cylinder, and then screws on the cap to secure the anatomy in place. Shivani and I were able to quickly create this mechanism on Fusion 360 and get it printed. The mechanism was successful, minus a few small changes that we will make next week.

This is the new attachment mechanism. The labia and hymen are on a table with a rectangular protrusion that allows it to fit into the cylinder. The circular ring screws on to hold the anatomy in place.
While we worked on this, Alex and Elise tackled other aspects of the project. Alex focused on finalizing the labia and hymen mold according to our client’s new wishes of a circular shape. We are still experimenting with different sizes of the mold, as we are aiming for a size that is both big enough to manipulate but also accurate to the anatomy of a young female. Elise worked on the base of our model. We are going to create an acrylic base that is easily sanitizable. Additionally, Elise is working on finalizing a notching system that will allow the model to lock in different positions. Both the base and notching system will be laser cut, so she is working in Adobe Illustrator to prepare the files with the base and notching system.
On Thursday, we met with Dr. Schmeler, a gynecologist at MD Anderson Cancer Center, to get feedback on our various synthetic skin samples. After talking with her, she indicated that Ecoflex 30 would provide the best tactile experience of the anatomy. She was very pleased with the visual appearance of the anatomy as well. Now that we have finalized our material, we can put materials testing aside and focus on accurately modeling the movement of the hymen and labia.

This was our setup for the meeting with Dr. Schmeler.
Overall, this week was tough; it’s difficult to work on certain things for a bit, only to pivot to something completely different midway through the week. However, I think our u-turn was ultimately necessary in equipping us to finish our project on time. Despite our crazy week, we left feeling optimistic about our plans moving forward, and we truly believe we can finalize a viable pediatric pelvic model by the end of the internship. Stay tuned for the final two weeks to see how our project wraps up!
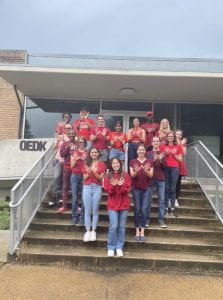
All the interns wore red one day this week, so we took this cute heart picture. Go Owls!
See y’all soon,
Shannon