This week was pretty amazing. That is really the only way I know how to sum it up. My team worked extremely efficiently and accomplished more than I could have ever imagined, AND we had a great time doing it! Thinking about it puts a huge smile on my face.
Monday, we essentially started from scratch. At the end of last week, we were told that our budget was significantly larger than we had previously thought for the final prototype, so we went back to the drawing board over the weekend, thinking of new ideas and revisiting old ones. By the end of Monday, we had an outline of what we wanted in our final prototype and had begun to construct a mid-fidelity prototype. The new design consists of 2 bellows (one on each side) with a rocking mechanism in the middle, so the woman rocks her feet back and forth to generate negative pressure.
We went to Home Depot to pick up some supplies this week to build the device, and it was a great adventure! Nehuwa said that it was completely different from hardware stores in Malawi, where there is a counter that you go up to and ask for whatever you need from the worker. We went up and down the aisles searching for buckets and rods and plungers. That’s right, plungers. Instead of buying actual bellows, we decided to buy mini plungers and attach hoses to the hollow handles. This was very inexpensive and convenient to find. Also, they provide an impressive amount of suction!
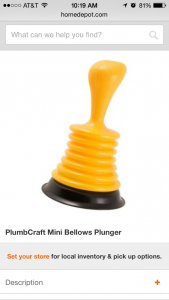
As the week went on, we split up the work to complete the prototype, although we worked with each other on each of the design blocks. Nehuwa focused on the breast shields, creating a long and smooth enough nipple channel. Mikaela worked on assembling the pressure generation system, connecting the bellows and the bucket with the board to rock back and forth. I doubled down on the part that connects the breast shield, collection container, and pressure generation system. We decided to use the Medela duckbill valves based on cost and quality. I tried multiple ways of connecting the pieces and, in the end, decided to use 2 pieces of PVC at a 45 degree angle with a hole for the tygon tubing. I removed one of two seals on the Medela valve so it fit around the edge of this ½ inch diameter PVC. I cut a hole in the cap of a plastic water bottle and secured the valve through this hole so the collection container could simply be a plastic water bottle. I then protected the hole for the tubing by installing a barrier composed of thicker tygon tubing. The entire system is very low-cost and all parts except the valve are available in Malawi. By Friday morning, we had each finished our design block so we assembled the prototype. We were surprised by how easily it functioned – very little work was needed to generate pressure.
After assembling it, we tested it on our faces, like the true professionals we are.
Actually, this is how we felt the pressure from the Medela and Ameda pumps, so we could roughly understand whether or not it was generating enough pressure. We realized that it more or less was generating sufficient pressure!!! After we found out that it generated pressure, the other interns wanted to feel it for themselves. The absolute highlight of my week was when Florence tried it on her face. Initially, it did not have a complete seal, so she did not feel the pressure. However, once she adjusted the breast shield’s position on her face, she felt it immediately and was completely shocked! It was hilarious.
After a brief period of celebration Friday afternoon, we went right back to the grindstone, beginning on our second prototype with smiles that spread ear to ear.
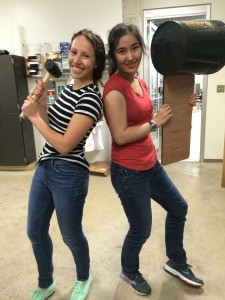