During the last week of the internship, we had the opportunity to present our project pitch and prototypes at the 2022 Rice360 Internship Innovation Showcase, held in the BioScience Research Collaborative (BRC). We decided to have our medium-fidelity prototypes for the Bucket Building and the Unidentified Fixed Object (UFO) finalized by the end of Week 6, so that we could focus on the Fusion360 animations and perfecting our project pitch during Week 7.
Frontloading the prototypes as much as possible definitely served us well, because we discovered an error over the weekend with the circuitry in our prototype of the UVC door. We created this larger-than-life compartment to demonstrate how the UVC would turn off as soon as the compartment was opened. This helps ensure the user’s safety, since they won’t be exposed to UVC light, while also ensuring power efficiency. Although the team was able to correctly install the circuitry and LEDs with the help of our Technology Lead Alois, the light strip didn’t work when the compartment was right side up. (But it was fully functional when the compartment was placed on its other five sides – go figure)! We were all befuddled, until Peter and Alois figured out that the issue was with a spring in the battery pack powering the LEDs.

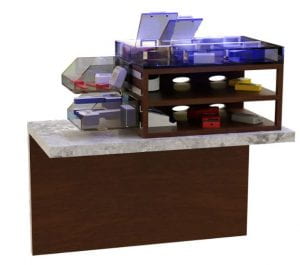
Once we moved past that roadblock, the rest of the week leading up to the showcase went relatively smoothly. On Thursday – the big day! – we arrived early at the BRC to set up, eat lunch, and practice our pitch in the auditorium. It was really great to see everyone’s projects come together so well, and I enjoyed watching my peers proudly present their hard work from the summer. I’ve been working hard to improve my public speaking skills, and I was touched to hear from Ms. Volz and Ms. Mitchell that they were impressed by our presentation. I’ll definitely be reaching out to Ms. Volz during the school year for more public speaking tips, so I can continue to push myself in an area I’m uncomfortable with (I hear practice makes perfect, or something close to it).
I’ll be back for one last post soon to reflect some more on my internship experience (no spoilers, but I’m really grateful to have been a part of it). Until then!