Week Seven: July 20, 2015
Mikaela Juzswik
Home stretch, people.
The overwhelming success of Week 6 behind us, the team and I jumped straight into the last two weeks of this project with a ton of things still to be done. We began running some tests on the first prototype, and that yielded some interesting results: although the suction that we’d quasi-tested using our faces felt about as strong as the Medela hand pump we were using for comparison, the numbers begged to differ. The Medela hand pump generates a pressure differential of about 220 mm Hg, while our first prototype only generates approximately 125 mm Hg. We were still leaps and bounds ahead of any of the previous Rice-built models (which capped out at about 50 mm Hg), but nowhere near the range we’d set forth in our design criteria. We attributed a fair portion of this pressure loss to imperfections in the build phase: we hadn’t fully sealed off the bellows from all possible air leaks, some of the operation was still unstable, and the connections we were using weren’t properly installed. We also did a quick cost analysis of the first prototype and discovered that there were a ton of hidden costs that we hadn’t accounted for. The hinges that we’d quickly installed into the sides cost around $6, approximately a quarter of our $25 budget, and the bolts, washers, and nuts that we used cost around the same. Although the prototype didn’t look expensive, it actually clocked in at around $40—about the same price as a Medela hand pump. Oops.
With these tests in mind, we started making a second, higher-fidelity prototype that addressed the issues we found in the first iteration, focusing primarily on instability of the pumping mechanism, sealing off air leaks in the bellows, and decreasing cost. Our team ended up splitting to divide and conquer again—I lead the charge on the second prototype with some handy assists from Leah, while Leah and Nehuwa largely focused on perfecting the breast shield/valve system. The valve system proved relatively straightforward, with fine-adjustments being made on the systems built last week, but the breast shields ended up being quite tricky. How do we build a low-cost, easily-adaptable (there are currently five widely-used sizes of breast shield), medical-grade technology using water bottles and PVC? We ended the week a little stumped on that one, but we’ll hit it again in the final days.
The second prototype was designed to address most of the problems that we saw with the first. The hinges, while nice for folding capabilities, added a major point of weakness to the device, as the bucket was constantly being pulled outward with each use. Also, as previously mentioned, they cost a fair amount—with the hardware required to install them, they clocked in at around $12, approximately half of our budget. No good! We sought to eliminate this issue by forgoing hinges entirely, and instead having a removable board that spanned the entire device—also conveniently removing the issue of the boards sagging in their hinges. We modified the attachment system for the plungers to the base as well, adding in some elastic bands and thickening those supports instead of using the previous method of duct-taping everything. We also selected and used a stain on the wooden pieces, as this would overall make the device easier to clean in the event of any unwanted spillage.
The final result turned out quite nicely:
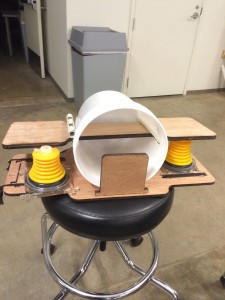
We did some further analysis on our prototype, and we reached a few conclusions, some good and some bad. The suction potential was definitely better reaching around 200 mm Hg at its peak, but since we’d sealed off the air leaks, it was actually much harder to obtain maximum suction than it had been before, meaning users really had to work at times to get the full vacuum. In addition, the method of securing the bellows to the base, while better than the first prototype, still wasn’t terribly secure, meaning the whole thing shifted around quite a bit when in use. However, we’d nearly halved our cost, bringing our device to within-budget at $22. Huzzah!
Overall, more improvements than bad things, so we can maintain our positive outlook for now. There will be a lot of work to do in the last few days, but I end up saying this every week, so I feel like that phrase is starting to lose its charm. Onward for the final push!