This week is when we are expecting to ship out the next round of units to Malawi! Since there have been quite a few revisions since the last model, I retrofitted some units from 3SD and sent those over to Kelley at Rice. In return, she will send back the units that she has on hand so that I can update them.
There’s been quite a bit going on this week due to the big deadline, and this past Thursday, I made a drive up to Sacremento to visit Pride Industries, the manufacturing company that is producing the Pumani units. The primary purpose of my visit is to make sure the revisions to the units are being made correctly and ensuring that the units are being thoroughly tested to be ready for clinical use. Since I’ve been working so closely with the Pumani units and am most familiar with all the revisions, Robert felt I could make the trip alone. As it turns out, there were a few minor issues to be resolved, so I’m extremely glad I was able to be there in person to work through them. Along with Mark, James, and Dennis, who are the primary technicians behind the manufacturing and testing processes for Pumani, I was caught up to speed on where they were in the process thus far. Unfortunately, there were some delays due to nonconformist issues with the suppliers that Pride was working with. For example, many of the packaging boxes came with weakened corrugation in a few areas and had to be remade. After communicating with the Pride team, I realized that much of their production is dependent on paperwork being processed and approved. (I’m discovering more and more how prevalent this is). However, upon my arrival, Pride was already well into production.
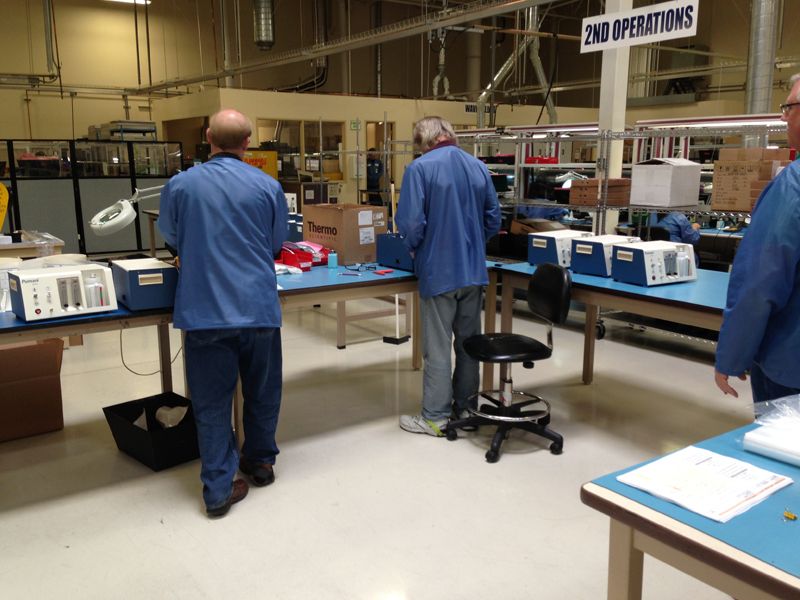
I went through the units that were being completed and inspected them for correct assembly and appropriate resolution of minor problems from the previous revision. I knew this was necessary since the tubing inside the units is actually very sensitive to orientation and placement. If they are not inserted or positioned the correct way, there is an increased chance for kinking. I found no problems at all in their assemblies. Pride also successfully resolved a minor glue issue that we found in the last units. In this round, we also made the spare parts kit inside the Pumani more secure by fastening them with hook-and-loop instead of double-sided tape.
After witnessing the production line, I discovered how detail-oriented and meticulous their process is. I briefly touched on the vision of the company in a previous post: to provide jobs to those with disabilities. In this regard, they’re extremely successful. As a result, their process must be very well documented and well thought out to ensure consistent, quality builds. For this purpose, they have made many clever building fixtures. For example, some laser cut pieces are used to help in cutting tubes exactly the correct length or act as guides for placing labels.

After quality checking the units for correctness in assembly, I observed as James (the testing engineer) ran the analog and digital pressure tests for every unit. The results are all printed, documented, signed, and filed away. The tests that are being run are the same as the ones I had been conducting at 3SD, so it was very helpful for me to be able to look at the quantitative results and graphs to ensure conformance.
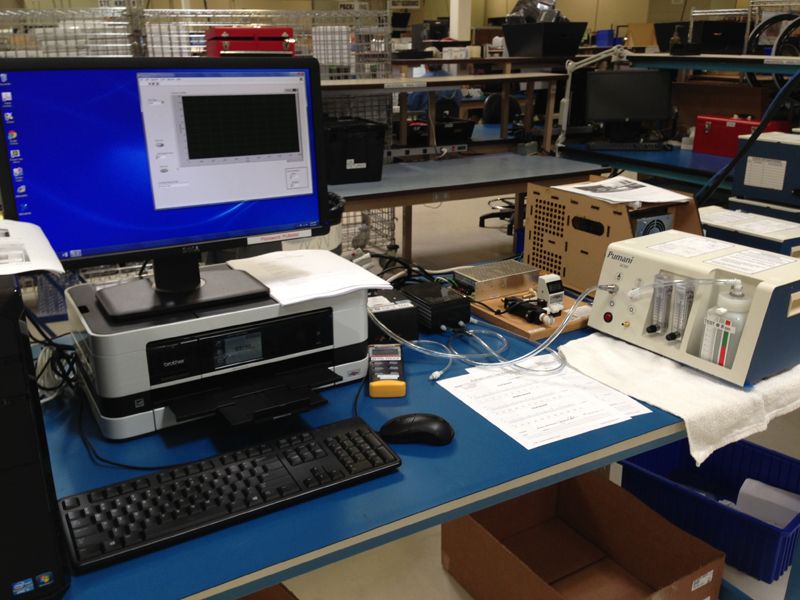
The testing went well, and I thanked Pride for allowing me to watch their process and keep an eye out for potential problems. I then made the drive back home, which somehow seemed much longer than the drive there. It’s a little surprising how much energy driving long distances can take out of you!